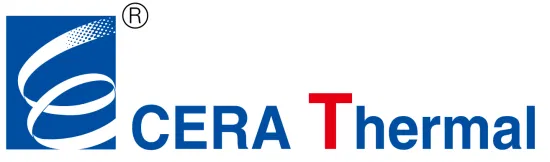
CT 1260 Refractory Fireproofing Ceramic Fiber Insulation Board
Basic Info.
Model NO. | CT-1260 |
Rupture Strength(MPa) | 0.5 |
Ignition Lost (at 1000ºCx5hr) Lol% | 8 |
Thermal Conductivity (W/M.K) | 0.132(600ºC), 0.19(1000ºC) |
Color | White |
Transport Package | Paper Carton /Pallet |
Specification | 6/13/25/50 |
Trademark | Cera Tec |
Origin | Jiangsu |
HS Code | 6806101000 |
Production Capacity | 1000 Pieces / Week |
Product Description
CT 1260 Refractory Fireproofing Ceramic Fiber Insulation BoardProduct Picture
- All kinds of ceramic fibre board adopt ceramic fibre which is in Corresponding temperature level as raw material, through the large automatic vacuum filter molding machine to shape them, then they will be done after special baking.
- The product with good toughness and strength appears flattening and the ceramic material distributes uniformity, it also has excellent Thermal insulation performance.
- Heating is not inflated, light, construction convenient, free shear and bending, is the ideal energy-efficient insulation materials of a furnace, piping and other equipment.
Product Features
- Low thermal conductivity and ow heat storage.
- High temperature stability and resistant to thermal shock.
- High crushing strength and good toughness.
- Allow machining and cutting, easy application.
- Resistant to airflow erosion.
Data Sheet
Type | CT 1100 | CT 1260 | CT 1360 | CT 1430 | CT 1500 | CT 1600 | CT 1700 | CT 1800 |
Classification Temperature ºC | 1100 | 1260 | 1360 | 1430 | 1500 | 1600 | 1700 | 1800 |
Color | White | White | White | White | Light Green | White | White | White |
Density(kg/m3) | 250-400 | 300-600 | 400-700 | 500-700 | ||||
Linear Shrinkage After Firing (ºCx24h) | ≤4 (1000ºCx24h) | ≤4 (1200ºCx24h) | ≤4 (1300ºCx24h) | ≤4 (1400ºCx24h) | ≤4 (1400ºCx24h) | ≤1 (1500ºCx6h) | ≤1 (1600ºCx6h) | ≤1 (1600ºCx6h) |
Ignition Lost (at 1000ºCx5hr) Lol% | 8 | 8 | 8 | 8 | 8 | 8 | 8 | 8 |
Thermal Conductivity (W/m.k) | 0.132(600ºC) 0.15(800ºC) | 0.132(600ºC) 0.19(1000ºC) | 0.132(600ºC) 0.19(1000ºC) | 0.132(600ºC) 0.19(1000ºC) | 0.132(600ºC) 0.19(1000ºC) | 0.16(800ºC) 0.20(1000ºC) | 0.16(800ºC) 0.20(1000ºC) | 0.20(800ºC) 0.23(1000ºC) |
Rupture Strength(MPa) | 0.5 | 0.5 | 0.5 | 0.5 | 0.5 | 0.8 | 0.8 | 0.8 |
Typical Application
- All kinds of industrial furnace hot face and back face insulation.
- Kiln linerof the high-temperature furnace, kiln cars, door damper, furnace temperature to separate plate.
- Deep processing products molding mould, like Craft glass etc.
- Astronavigation,Shipbuilding heat insulation,fireproofing, sound proofing, insulation.
Customers
Company Profile
Jiangsu Cera Thermal Technology Co., Ltd. is formerly known as Nanjing Cera Material Technology Co., Ltd.The main business of our company includes refractory materials production, furnace lining design and construction of high-temperature thermal engineering, furnaces equipment, research and development and sales of refractory material. Through years of cooperation with the British Morgan Thermal Ceramics,we have accumulated rich experience in a good deal of engineering projects. We can provide our customers with all kinds of high quality products, professional and customized products and engineering services according to the actual working condition and requirements of each customer, in order to meet customers' increasing demand of energy-saving.
Our tenet is: quality and credibility is fundamental, technology and service is the life.
- 2002 Established Nanjing Cera Material Technology Co., Ltd.
- 2005 Set up Nanjing workshop.
- 2009 Started Suzhou SLMC Thermal Insulation Materials Co., Ltd.
- 2010 Started Shandong Zibo Baoyang Refractory Fiber Co., Ltd.
- 2013 Started Thermaltec Insulation(Zhejiang)Company Limited.
- 2013 Started Jiangsu Cera Thermal Technology CO.,LTD
We obtained the quality system certification GB/T 19001-2008/ISO 9001:2008.
High-tech enterprises are under declare.
Certifications
Why Choose Us ?
1. Thermal calculation, material selection support.
With advanced calculation software, it can calculate the heat storage loss and heat loss of
the kiln according to the temperature in the furnace, the working environment of the kiln,
and the economic selection of materials.
2. Process design.
Professional lining design team.
3. On-site guidance.
Have a rich team of on-site construction experience to provide customers with excellent
construction site guidance.
4. Installation Supervision.
Possess professional construction supervision ability, can provide professional construction
supervision service for furnace lining installation and constructio.
5. Special application consultation of thermal insulation materials.
We can provide technical support for customers and solve the difficulty of applying special
thermal insulation materials.